What student housing developer UTILE can teach you about modular construction
Student housing developer UTILE can teach the industry a thing or two about modular construction – including what it’s going to take for it to hit the mainstream in Canada.
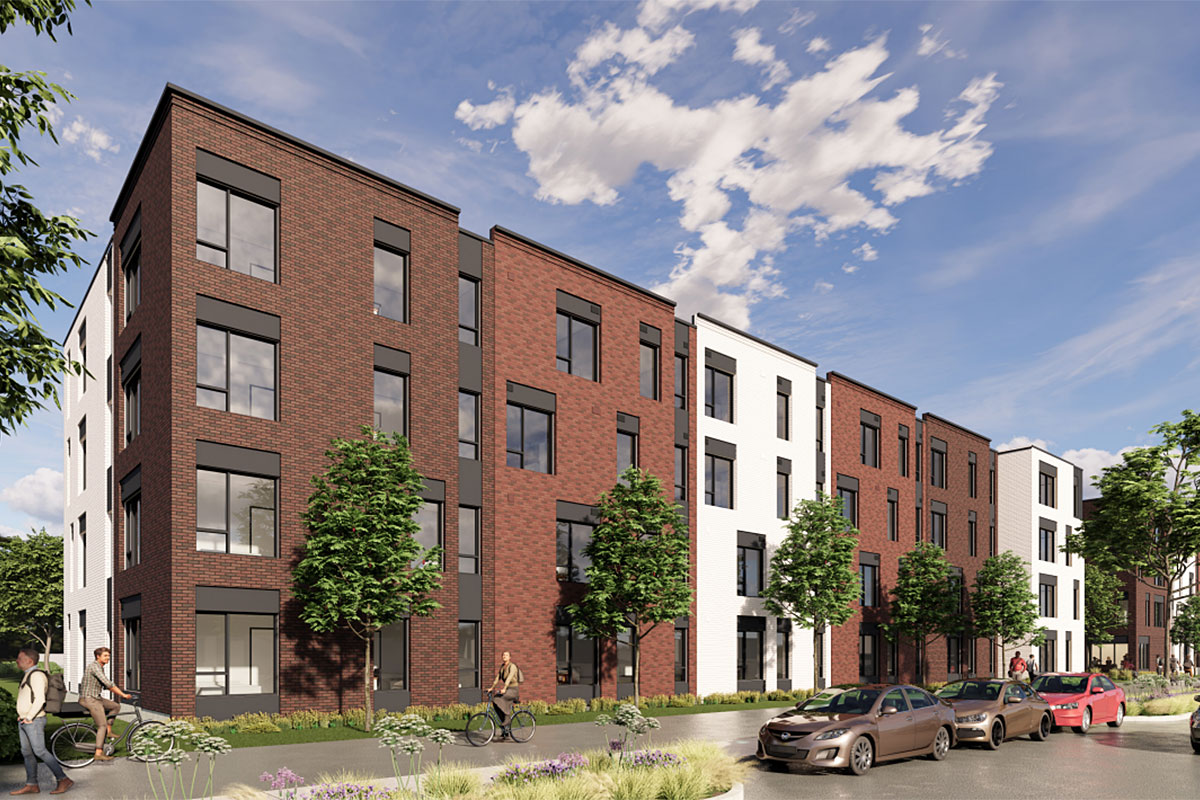
UTILE, a finalist in this year’s CMHC Housing Supply Challenge, questioned why, despite offering significant advantages, multi-residential modular construction only accounts for a very small share of the residential market in Canada. So in 2024, the Montreal-based non-profit kicked off its first modular construction project, a 155-unit midrise complex in Rimouski, Que., to see how modular construction could work more effectively. What UTILE learned might surprise you, but thankfully its key findings can be successfully replicated for any type of modular housing development in Canada.
“In the past seven years, construction costs in Canada have increased by more than 50%. It is simply impossible to overcome the affordability crisis without tackling the rising costs of construction. In that regard, modular construction has enormous potential,” says Gabriel Fournier Filion, UTILE’s CEO.
Modular construction enables project owners to shorten development cycles by approximately half and therefore build twice as many housing units per year, yet remains significantly underexploited. While faster than traditional construction methods, UTILE found that it can be costlier than traditional projects and is perceived as riskier by construction stakeholders. So, the question that begs an answer is why isn’t modular construction cheaper?
Three factors making modular construction expensive
UTILE identified three reasons why modular costs more than traditional construction. The first reason is that subsequent projects rarely proceed because modular-building manufacturers currently focus on single-family housing which has higher margins but lower volumes. From UTILE’s experience, this creates two new issues.
- Modular-building manufacturers won’t invest in their production capacity and efficiency if there is no pipeline of guaranteed deals.
- The experience acquired throughout the production chain during a modular project is not taken advantage of, so opportunities to reduce the costs of subsequent projects are lost.
The second reason is that standard construction contracts are poorly adapted to modular construction since there are multiple parties involved, including those doing part of the assembly work in the factory and those working on site. UTILE found that as a result, manufacturers, general contractors, and subcontractors will increase their bids to cover their risks in case of warranty claims.
Canada’s construction industry’s lack of experience with modular presents the third challenge and increases costs. Here’s why. The assembly details of a prefabricated project are different from a conventional project and are unknown to professionals, general contractors, and subcontractors, leaving them to guess. Also, the scope of work on-site is not fully understood by the stakeholders involved. This leads to them substantially increasing the safety margins in their bids because they cannot accurately estimate the time and materials required.
Success found with consortium model
Based on its findings, UTILE has brought together a consortium of stakeholders – including a prefabricator, general contractor, architects, and engineers – to collaborate on and repeat several consecutive projects. This new consortium model from UTILE focuses on building industry partnerships as a way to create more market certainty and improve efficiency with every project completed.
UTILE has also committed to producing at least one large-scale, multi-residential project (70 to 310 housing units) per year for the next five years. By committing to building several hundred modular housing units, UTILE is encouraging the prefabricator to invest in its plant to increase its efficiency and production capacity, which the non-profit sees as a benefit for the broader industry.
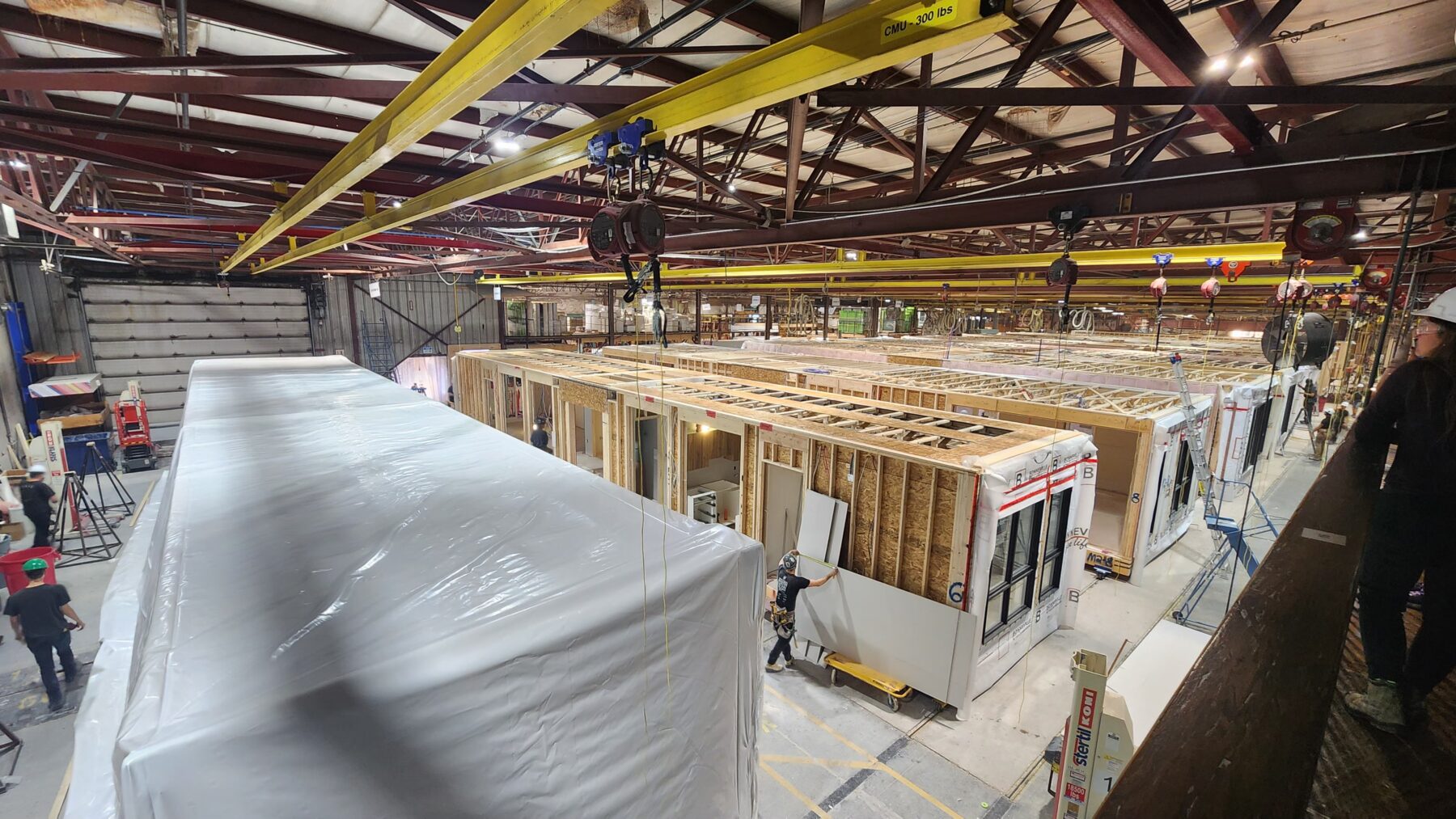
UTILE is also developing new contracts specifically for modular construction to clarify the legal responsibilities of each stakeholder involved – from the factory to the construction site. Stakeholders will then better understand their legal requirements so they do not needlessly inflate their bid to compensate for risks that, in reality, are either mitigatable or assumed by another stakeholder.
UTILE is also aiming to cut the costs of modular construction by 10 to 15 percent compared to traditional means. The non-profit will carefully document the costs of all stakeholders in the value chain to target measures and reduce prefabrication costs. Very importantly, this documentation implies that all of the involved players will be transparent about their costs.
Educating subcontractors who are bidding on modular projects so they can understand the exact scope of work to be done is another UTILE priority. The non-profit is developing plans and specifications – including an explanatory video via BIM modelling – so it can predict the cost of each subcontractor to the nearest dollar.
“As a non-profit with a high development volume, UTILE is uniquely positioned to finetune a model that makes modular construction highly scalable and to disseminate it among the industry,” adds Fournier Filion.
UTILE to open source its key learnings
To help other developers in Canada more effectively adopt modular construction, UTILE’s modular pilot project will be the subject of a white paper that will be written by an external firm (MNP). It will be available in Fall 2025 and be widely distributed.
To ensure you don’t miss out, you can signup to receive a free copy of UTILE’s white paper featuring its key findings on modular construction, by contacting: modular@utile.org
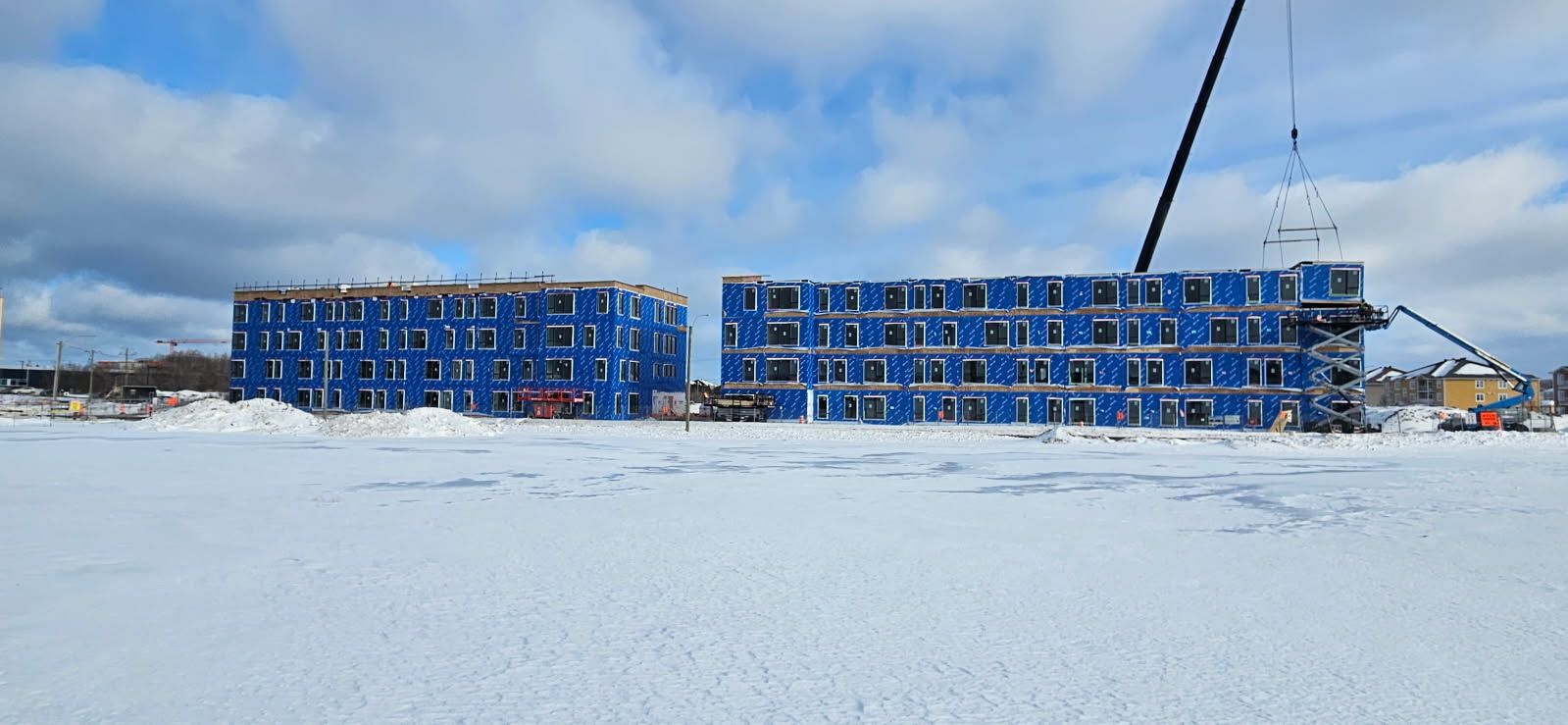