Untangling construction’s supply chain problems
Experts talk stockpiling, bad owners, chaos theory and how we might create more sustainable supply chains.
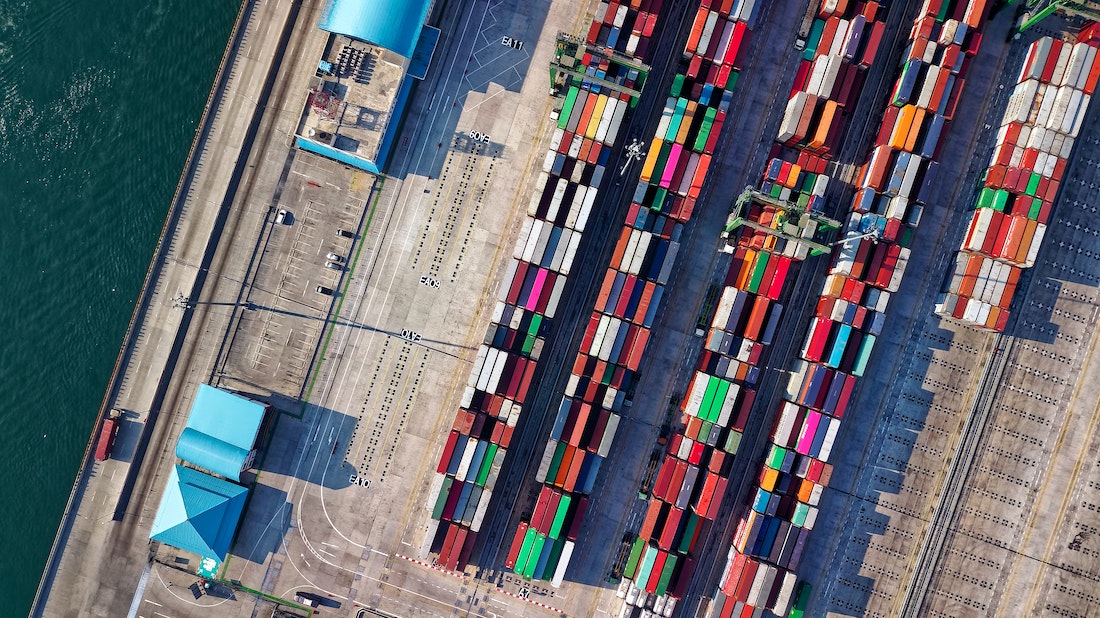
Shipping containers are sorted at a port.
It all started with joists.
About a year and a half ago Josh Gaglardi, president of Orion Construction, saw that the lead time for ordering joists had jumped from an average of 8-12 weeks to as much as 24.
“That was the first canary in the coal mine,” said Gaglardi. “Now a lot of other items are hard to get: breakers, distribution equipment for electrical work, packaged HVAC units. The list is getting longer and longer.”
Shifting schedules around
Timelines for some parts are as long as six months. Roughly a year ago, Orion began strategizing ways to get ahead of these setbacks and lead times. They asked clients to hedge on inflation and costs to secure product for their project. Procurement, engineering and detailed design were pushed ahead of schedule so materials could be ordered earlier. Orion then stored these materials on site or in a warehouse.
“That was our major mitigating strategy to hedge against inflationary pricing increases and long lead times and we had a lot of success with that on projects,” said Gaglardi. “It definitely impacted our corporate strategy and has caused us to be more creative in our approach.”
The B.C.-based construction company has now found itself regularly warning clients that there may be supply chain issues in schedules.
“At the beginning it was tough because nobody understood what was happening,” said Gaglardi. “It was a new problem for a lot of people and it took a lot to explain. But the media publicized it so it got easier and easier. People knew before I even had to tell them.”
Gaglardi has been in construction for roughly 20 years and has never seen supply chain issues like today. The only other issue of note was six years ago when a steel tariff dispute with the U.S. caused prices to spike.
“That affected us and it is comparable but not the same magnitude,” said Gaglardi. “You look around now and it’s a new thing every day.”
Despite these challenges, Gaglardi remains optimistic.
“I think there won’t be as much general opportunity because the economy is slowing, you can definitely feel that and read that too,” he said. “But I think we are forced to be optimistic in the business. There will be opportunities in 2023. The building industry will still exist.
Stockpiling materials
In Alberta, the Calgary Construction Association (CCA) attempted to create a living document of specific supply chain issues in the region to assist builders, but the problem became too difficult to keep up with.
“Frankly things got so volatile, so unpredictable, so multifaceted,” said Bill Black, CCA president. “Every 48 hours something else was going on. It was too much of a moving target. At the same time the industry in its own form had already started to adapt and work around things.”
Black said companies who had the capacity to do so began stockpiling key items.
“Rather than ordering by the project, they were carrying inventory at their own cost – the kind of stuff you would use on every job,” said Black.
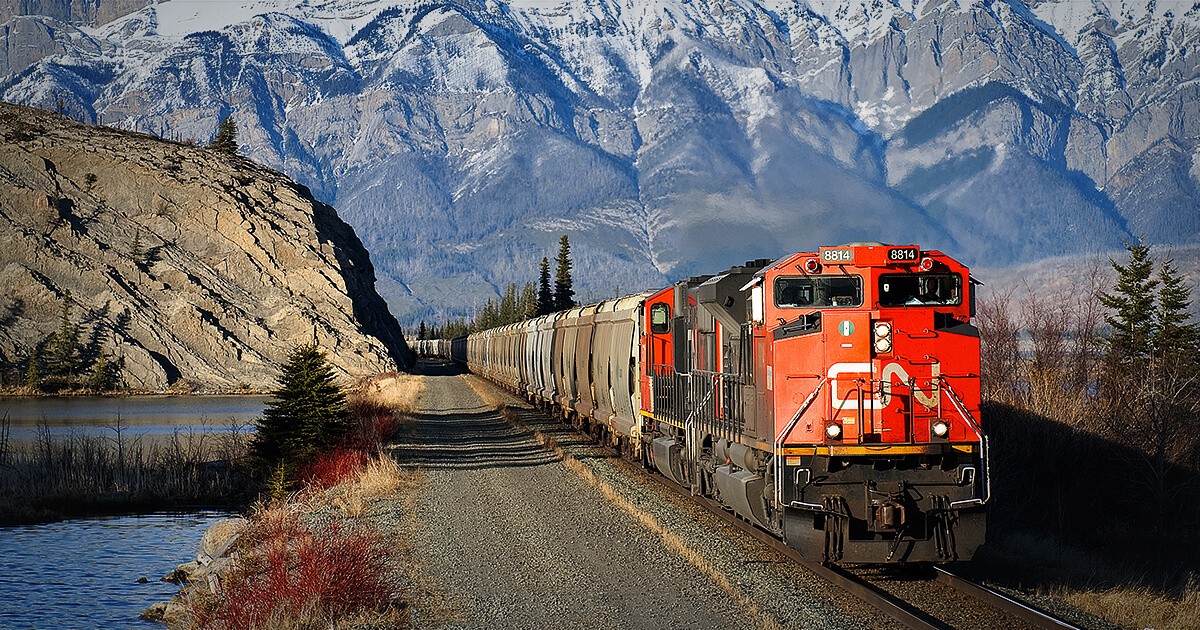
These included common kinds of wiring and commonly used rooftop HVAC units. These units even recently have seen lead times as high as 52 weeks.
“The benefit is they have an inventory that allows them to create predictable schedules and charge whatever the market rate is which probably covers carrying costs,” said Black. “However, you have to have the cash flows that support that and potentially a bank that understands that you have had to shift to this static inventory model.”
However Black noted that this has likely hampered smaller companies’ ability to hold the price as they aren’t able to place orders and stock products for extended periods of time. But he believes the larger problem has been higher up the chain.
Unreasonable owners not helping
“Not all owners have been willing to accept the reality of this and are not willing to pay for products or materials ordered early, or not willing to pay for stuff that hasn’t been installed,” said Black. “They were already doing that before supply chain issues.”
He noted that public owners have been worse than private ones.
“They just seem to think they are allowed to demand the untenable and they seem to believe the industry is so desperate that there is an endless supply of companies willing to bend to them,” said Black. “The challenge is that some people might be willing to take the risk and it might backfire.”
He believes it’s likely that private owners often have people internally who understand the construction industry and have more respect for what’s going on and how they can contribute to the solution.
“When it comes to public owners we see less and less people at municipalities and with the province that actually know the industry to any level of detail and have bureaucratic rules that have created an arms-length relationship between them and industry,” said Black.
Black said the result is more and more companies pulling back from working with these entities who he says have an unrealistic attitude around the level of risk that should be borne by Alberta builders.
“Not all owners are willing to accept the reality of this.”
Bill Black – Calgary Construction Association
Black expects the supply chain issues to persist for several more years.
“I think they will settle down, and by settling down I think lead times will become more predictable and reliable, but I don’t think they will ever be as fast as they used to be. I think prices will stabilize but I don’t think they will be back to where they were.”
He noted that one way to stabilize the chain is to bring the source of products closer in areas that are more politically stable. But overseas products are often much cheaper.
“I think you will see a number of companies near-shoring and moving manufacturing,” he said, noting that this cuts down on risk and also one’s carbon footprint.
Canada working on national supply chain strategy
Supply chain issues have become such a national issue that they caught the eye of Ottawa.
This fall the National Supply Chain Task Force, which was formed by Transport Minister Omar Alghabra in the wake of the COVID-19 pandemic, released its final report. The task force wrote that a common theme they found was the struggle of both government and industry to cope with uncertainties arising due to critical factors such as rapidly changing trade patterns, human- and climate-caused disruptions, shifting geopolitical risk, and increased consolidation in major transportation modes.
“As a medium-sized player in the global market, Canada is finding it difficult to overcome these challenges, which have exposed and exacerbated longstanding weaknesses in the Canadian transportation supply chain,” the report said.
Highlights of recommended actions in the report include:
- Easing port congestion.
- Addressing labour shortages and employee retention.
- Establishing a federal Supply Chain Office to unify relevant federal government activities.
- Protecting corridors, border crossings, and gateways from disruption.
- Developing a national transportation Supply Chain Strategy.
- Engaging the U.S. and the provinces and territories to achieve mutual recognition of regulations, policies and processes.
The Government of Canada stated that it plans to develop a national supply chain strategy informed by report’s recommendations
What exactly is a supply chain?
Gregory Paradis is a forest industry expert who uses mathematics and computers to model interactions between forest ecosystems, industrial supply chains, governments and society.
He described the supply chain as a network where you need uninterrupted flows – from wherever they are coming from to wherever they are going.
“Think of it as an electrical grid, or network of connected machines, or a network of pipes that form a water system. All those networks are basically made up of arcs and nodes,” said Paradis. “Nodes are where things converge and flow. Arcs are where you travel. It’s things flowing from one place to another.”
He explained that when you have a large commodity market that’s driven by the lowest price, which characterizes construction, you end up with large suppliers that have a lion’s share of a very specific product.
Global commodity markets often trend towards hyper specialization and efficiency, which can leave little breathing room for when something catastrophic happens.
“With commodities you have these globalized markets and people from anywhere can push their product onto the market. If everyone is competing on price, what happens is people are outbidding each other to the point where they can’t bid any lower because price bumps into cost,” said Paradis. “When people start to play that game where the commodity hits the lowest price – where it’s cost plus a dangerously small margin – if they can get it a penny or two less per unit than anyone else, they become the biggest supplier and get the volume.”
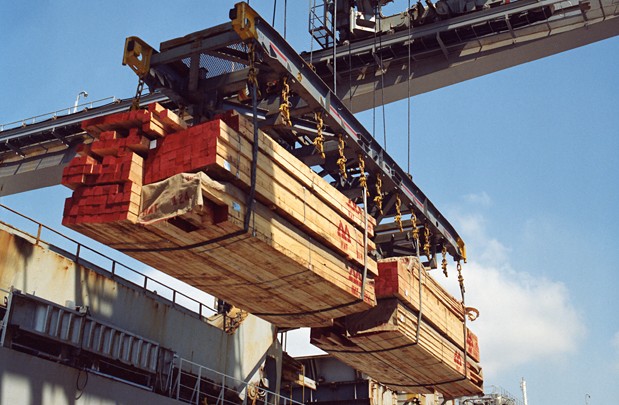
This happened to Canada’s lumber industry in the 1980s. Competition for generic dimensional lumber went global. This forced out smaller, flexible sawmills for large, specialized ones that could produce a very limited kind of product in massive quantities for cheap.
“Manufacturers that produce smaller volumes of higher diversity products cannot possibly match the unit price of someone that does one product in huge quantities,” said Paradis. “It’s the laws of economics. Economies of scale apply when you have fixed costs.”
How the chain gets broken
But to maintain their competitive advantage, these facilities have to operate at or near full capacity or they will lose their economic advantage and shut down or go bankrupt.
“Like a drag racer, it’s good at drag racing, but bad at everything else,” he said. “But if any of these places go offline or get disrupted, then you have an interruption in the flow. People look for alternative suppliers who either don’t exist or can’t absorb the demand.”
This is exactly what happened during the COVID-19 pandemic. Large facilities struggled to remain open due people being sick or in lockdown. The supply was squeezed, demand went up and so did prices. And nobody had stock saved up somewhere because storing large amounts of materials is expensive.
“If we had built a larger number of medium mills designed for flexibility and agility to run at 40 or 50 per cent instead of 80 per cent, then we would have fewer disruptions but higher prices,” he said. “What you saw during COVID was not altogether surprising.”
Even beginning to approach the issue of supply chains is immensely complex. Paradis said that just the wood product supply chain is made up of governments, resource extractors, product manufacturers, wholesalers, retail sellers, customers, builders, customers and more.
“All the different actors in the system are not working under a single emperor dictating how we feel and what our goals are. It is a highly decentralized and distributed system with distributed decision making,” he said. “Nobody got up one day and decided to build a supply chain. They just kind of happened for the most part.”
And even if one could get all these stakeholders into a room, coming up with solutions to supply chain disruptions gets even more complicated as the number of impacted stakeholders expands and unintended consequences can pile up.
Using computer modeling to improve the chain
Despite these challenges, there can be some success. Paradis has done extensive work with FORAC, a research consortium of forest products industry stakeholders.
“Everything they do is basically taking the forest industry’s supply chain and using math to try and find efficiency, resilience and flexibility,” said Paradis.
In more than 90 per cent of FORAC’s research projects, collaboration is identified as a way to improve supply chains.
FORAC found this to be true in work they did with the Swedish logging industry. Crews would harvest logs and then truck them to mills to turn into lumber. The companies coexisted in the same region where sometimes fully loaded rival company trucks would pass each other.
“That’s guaranteed inefficient nonsense. You are moving the same product in opposite directions. That whole chunk of road is a wasted trip,” said Paradis.
FORAC did complex modeling to figure out that if they could capture where the mill supply zones intersect, they could swap loads at the board instead of passing, decreasing everyone’s transportation costs. However, some would benefit more than others, which made for lots of negotiations. But eventually a deal was struck.
How chaos theory could help change it all
But Paradis wants to think bigger. A lot bigger. He’s begun to think about what a future, sustainable supply chain could look like and the effort that would take to get there.
It starts by understanding a bit about chaos theory.
“Chaos is not pure randomness. Chaotic systems are systems where 100 per cent of their behaviour can be explained with a set of rules, but chaotic systems are usually very complex. They seem to be mysterious, random black boxes,” he said.
An example of this is an ecosystem. Scientists don’t know how they entire system works but they seem to self-replicate and persist on their own.
“Supply chains and other systems like the forestry sector are systems so complex that they behave in ways we cannot fully explain or understand,” said Paradis.
But chaotic systems have an attribute called “strange attractor” where the system is orbiting around a current state and it is attracted back into itself.
“A strange attractor will keep being that thing until something nudges the system,” said Paradis. “Supply chains will keep doing what they do until nudged hard enough to skip over into the next puddle over. But once you get there, some of these systems are self replicating. It’s just getting there that is hard.”
Paradis believes that the apocalyptic threat of climate change could be a motivating force strong enough to nudge these systems into something better. He is currently working with the mining sector where many of the massive companies are self-declaring goals of reaching zero carbon emissions by 2050. But this will be impossible without buying billions in carbon offsets.
“What I am trying to do is get them on board for collaborative projects to design these transformative changes that bump us from one puddle to the next,” said Paradis.
He hopes that this could lead to collaborating on a more sustainable solution and provide a way to fund the shift.
“You have to have this grassroots groundswell where shareholders who control companies say we need this and this is why mining companies are declaring net zero goals. It’s what their shareholders want. The climate emergency may provide some of the catalyst necessary to achieve more sustainable supply chains.”