Ontario MPP goes from parliament to 3D printers
Ian Arthur left politics to start Nidus3D. Now he’s on a mission to transform the construction process.
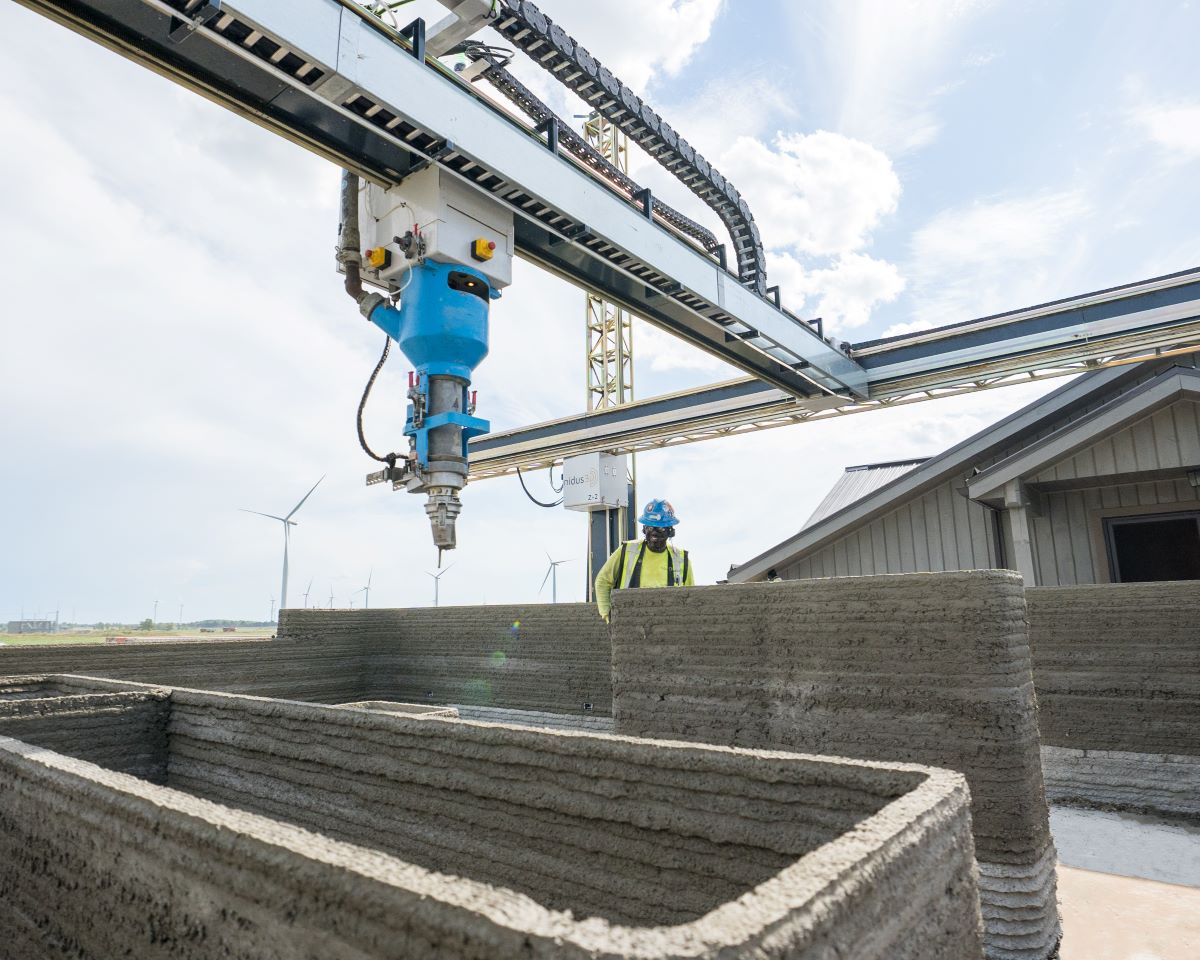
After serving four years as Kingston and the Islands MPP, Ian Arthur announced he would not be seeking re-election.
Ontario NDP leadership praised him for leading the battle to get more family doctors in Kingston, and by being an outspoken and purpose-driven advocate for action to address the climate crisis.
While he was proud of his political career, he wanted to do something bold in the private sector to solve some of the country’s biggest issues.
“Serving as MPP was a huge honour and I am happy I did it but I wanted something else,” said Arthur. “I was interested in getting back into the private sector and working in an area with room for innovation where I could be disrupted.”
When he saw the progress being made in robotics technology, he decided to tackle the issue of affordable housing and construction timelines.
“I’d been watching the technology for years and found it interesting and saw it reaching a tipping point where it was in a viable place to get into the sector and start building,” he said. “I think the link started while I was a politician. We did a lot of work on housing to increase availability of affordable housing. But we were faced with the reality that while there are some provincial policy levers we can pull that do have an effect, the breadth of problems facing construction were not going to be addressed by policy alone.”
Finding a robot
The same year he left politics he founded Nidus3D with Hugh Roberts. Roberts has worked in construction and development spaces for over a decade and has expertise in operations, R&D, sales, and strategy.
Their first step was building out a relationship with Denmark-based COBOD, the only company that manufactures a printer with the capability to match Nidus3D’s vision
The BOD2 printer’s modular truss structure presents several advantages for construction printing. The printer can be configured exactly to each project. It can also be upscaled and downscaled to suit larger and smaller projects that you may have in your pipeline. Nidus went to Demark to tour COBOD’s facility and watch the printers in action. The Nidus team then spoke with other COBOD customers about their experiences.
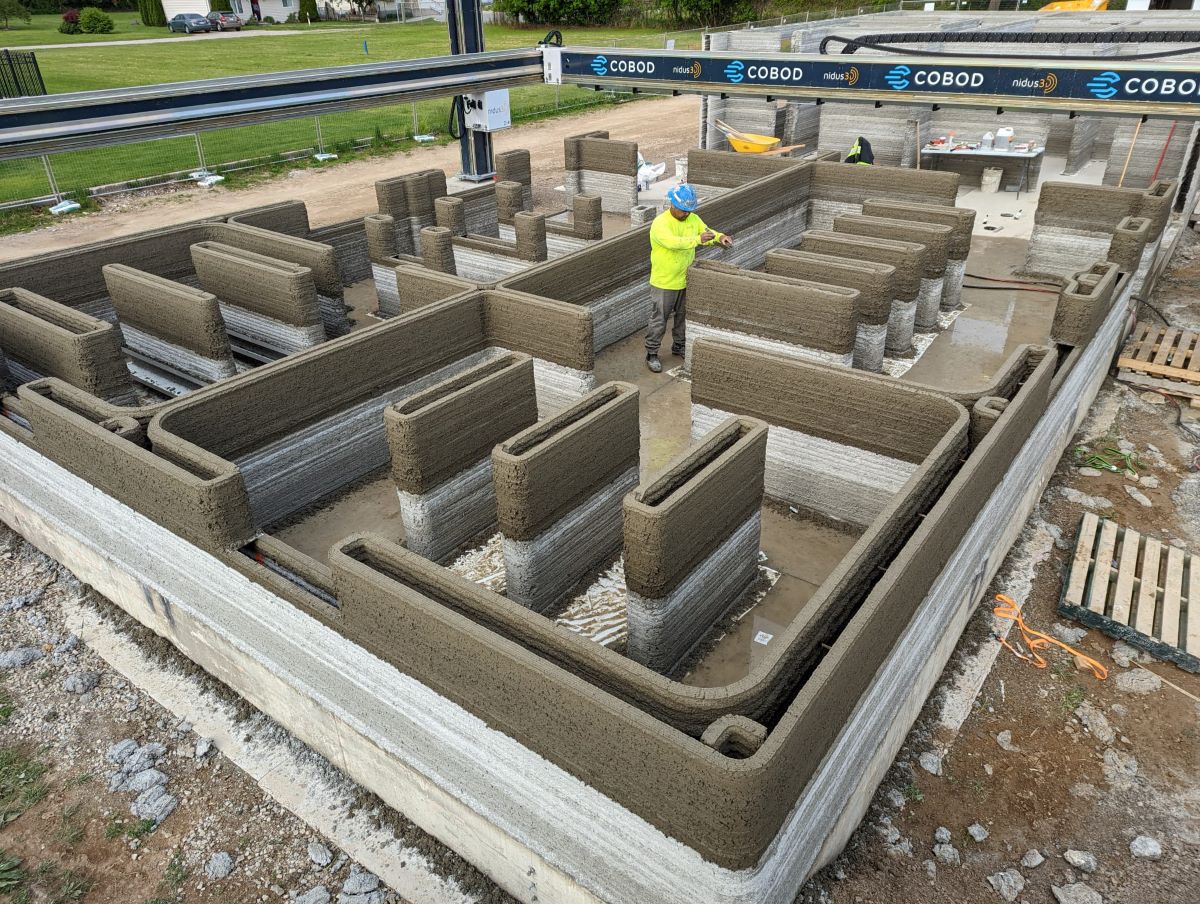
A ‘let’s get building’ approach
After that, Nidus3D scraped together some capital through a small pre-seed round to buy its first printer. It arrived last February for commissioning and the team started building. Since then, they have been making Canadian history:
- In partnership with Habitat for Humanity Windsor-Essex, and the University of Windsor, Nidus3D delivered North America’s first residentially permitted multi-unit 3D printed building. The build included four self-contained 560 square foot homes and was partially funded through Canada Mortgage and Housing Corporation’s Innovation Fund.
- Near Kingston, Ont., Nidus3D constructed the first-ever 3D-printed, multi-storey, mixed-use concrete building in North America. The 2,300-square-foot, two-storey building has a workshop on the ground floor and a residence on top.
Arthur explained that they are pushing the young, 3D-printed building industry forward not just because they want to, but because they have to.
“Hugh and I have driven a practical, ‘let’s get building’ approach’ while a lot of other groups in the sector bought the tech on a more experimental basis to play around a bit,” he said. “That is partially out of necessity. We did secure some small, pre-seed money, but we have to secure projects to secure revenue so it is a necessity for us to get out and deliver projects and that is a big factor pushing us forward.”
While these small, one-off projects are proving the viability of the technology, Arthur noted that 3D printing is far better applied on a larger scale.
“When we run our forward-looking numbers that’s where it really becomes cost competitive,” he said. “Our build costs on probably ten units and above per site is, I think, universally competitive with any technology in Canada and it’s only the beginning of this technology.”
This year the company plans to demonstrate the true benefits of 3D printing by spending roughly three months building a small, eight-building sub-division of about 24 units.
Addressing housing and labour issues
Arthur hopes that in the coming years, the technology can be used to address housing affordability and labour shortages.
“We make buildings with hundreds of different materials, thousands of components, tens of thousands of different process steps,” he said. “While we have had incredible material advances over the years, none of it has solved the process problem. I think this is one of the first things I have seen that addresses that process problem.”
Arthur noted that while Nidus3D’s projects get larger and more complex, the number of people required doesn’t increase.
“The best case scenario for training workers still won’t meet demand. This technology still has challenges, it still needs to improve and be optimized for efficiency, but it does begin to address that process problem,” he said. “When we do deploy a larger printer than we have now, it still only needs three people and as you scale that you begin to see what it could have a profound impact on the building sector and housing supply in Canada.”
Arthur doesn’t want to stop at 3D printing. While the goal is to scale the 3D business, he wants to look at ways to optimize the rest of the construction process, including mechanical systems, lighting systems, door and window installations, flooring and more. “How can we use technology to make these things faster to deploy? Maybe we rethink how we deliver those systems?” said Arthur. “We have to start thinking about building in new ways. The industry is scaling in inefficient, slow, complex and unpredictable ways. We can’t scale that, we will just fall further and further behind. If we don’t find groups and technology that break that down and rebuild from ground up will never solve these problems.”