Lafarge launches pilot project to store carbon in concrete
The system has the capacity to remove up to 1,000 tonnes of CO2 each year from plant operations, with potential to scale the system 10 times over the next year.
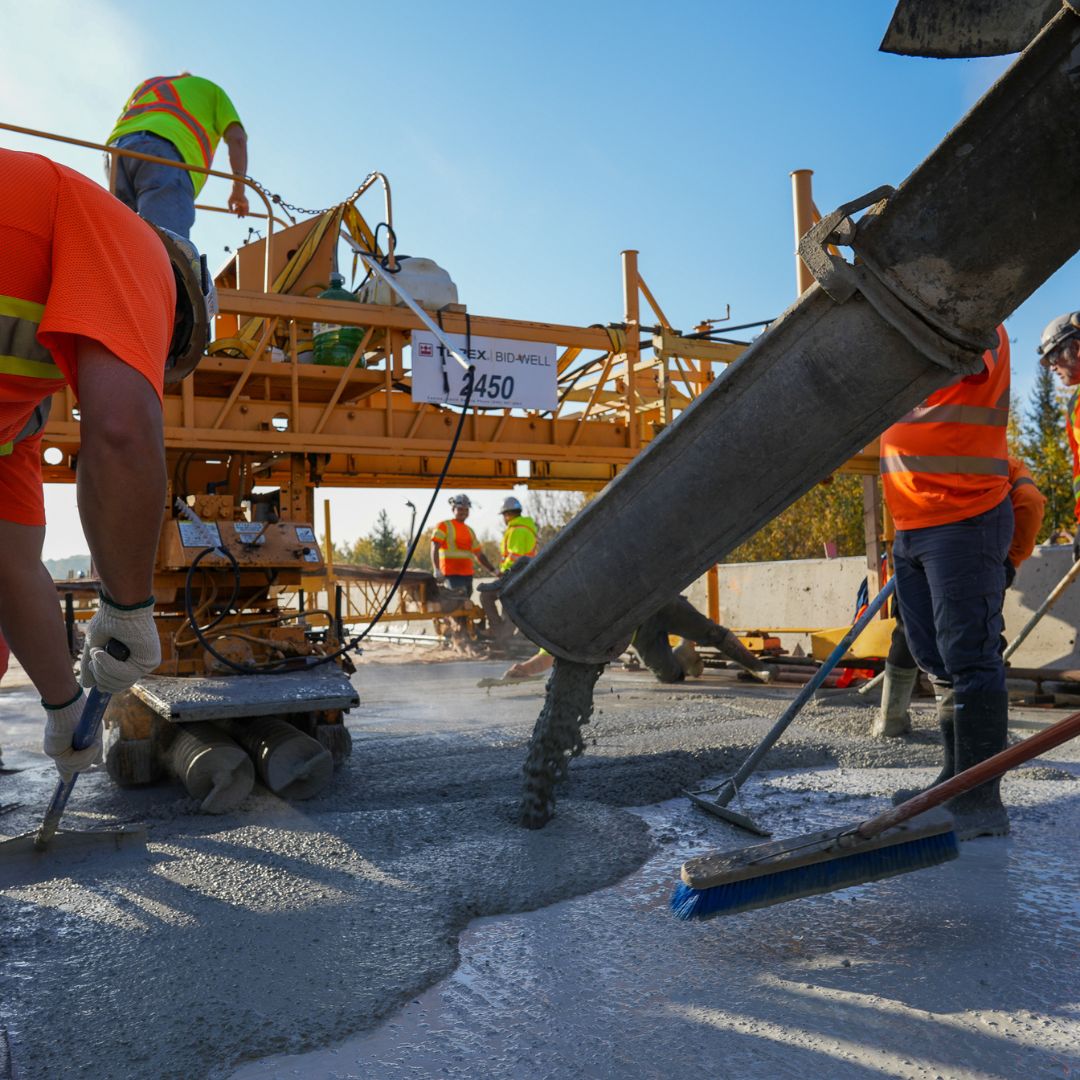
Key Takeaways:
- Lafarge and Hyperion are collaborating on a pilot project for a new technology called the Tandem Carbon Recycling System. This system captures carbon emissions from a cement plant and transforms them into high-performance minerals for sustainable building materials like low-carbon concrete.
- The pilot system has a capture capacity of 1,000 tonnes of CO2 per year,with the potential to be scaled up tenfold in the next year. This could lead to a major reduction in greenhouse gas emissions from the cement industry.
- The captured carbon is converted into minerals that enhance the strength and density of concrete. This paves the way for the development of more sustainable building materials with a lower carbon footprint.
The Whole Story:
Lafarge Canada Inc., a member of Holcim Group, and Canadian carbon technology innovator Hyperion Global Energy Corp, are launching Hyperion’s patented Tandem Carbon Recycling System pilot.
The process advances circularity by capturing and transforming carbon emissions into high-performance mineral components used to make sustainable building solutions such as low-carbon concrete and other materials.
The pilot project, currently in operation at Lafarge’s Bath Cement Plant in Ontario, involves the testing of Hyperion’s net-zero mineral solutions for advanced concrete such as Lafarge’s ECOPact, the broadest range of low-carbon concrete globally, which can lower embedded carbon between 30-90% compared to standard concrete without any compromise in performance.
The joint effort will further develop and scale Hyperion’s proprietary Tandem Carbon Recycling technology, a drop-in system that captures and transforms waste carbon emissions into high purity minerals that permanently store carbon. Hyperion says its novel reactive mineralization process achieves up to 98% capture efficiency of carbon dioxide emissions, producing innovative mineral components that enhance the density and strength of concrete, among other industrial uses.
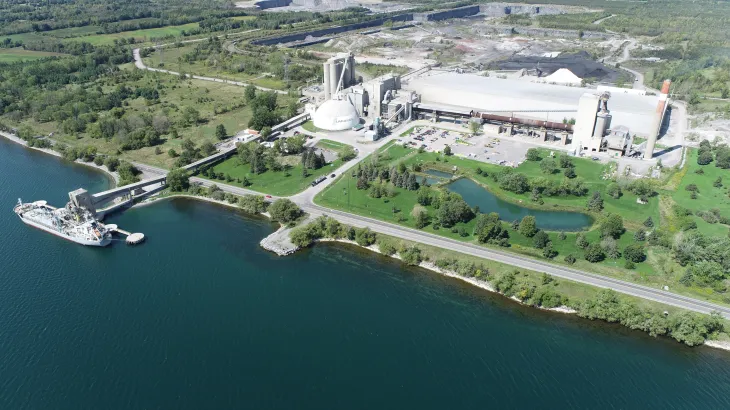
“Our collaboration with Hyperion marks an exciting milestone in our decarbonization journey and the advancement of our circular construction technologies,” said David Redfern, president and CEO of Lafarge (Eastern Canada). “We look forward to advancing our Net Zero strategy by leveraging carbon utilization technology like Hyperion’s, enabling us to further reduce CO2 emissions from our operations while at the same time producing innovative and sustainable building solutions.”
The pilot currently has the capacity to remove up to 1,000t CO2/year from plant operations, with potential to scale the system 10X over the next year. This represents a 500% scale-up of Hyperion’s novel technology since its original prototype as part of the global Carbon XPRIZE competition. The current system was fully manufactured in Ontario, working with local suppliers and trades, along with Hyperion’s team of industrial engineers.
“Working together with an innovative partner like Lafarge on this exciting pilot project allows us to apply our proprietary carbon recycling technology to large-scale industries, and make an immediate, measurable reduction on carbon emissions. At the same time, we are advancing our vision to offer a scalable and affordable decarbonization solution for industry, and a market-driven profit incentive on the cost of carbon removal,” said Heather Ward, CEO and Co-Founder of Hyperion.