Future of Work panel tackles technology and collaboration
Leaders say the industry must work together to succeed with housing, infrastructure and more.
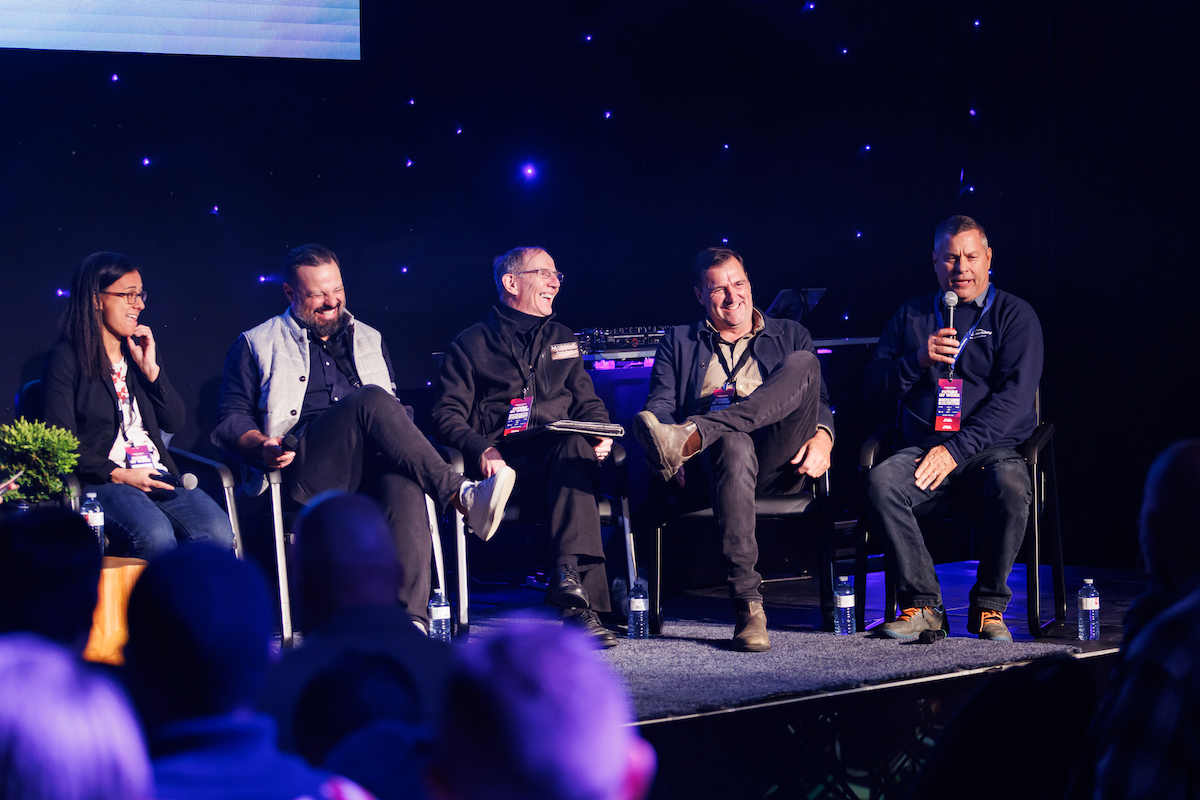
Key Takeaways:
- As projects get more complex, collaboration and technology are becoming more of a necessity to achieve success.
- Some industry leaders are moving towards standardizing components so the process can be sped up and industrialized.
- Panelists strongly encouraged government officials, trade contractors, project owners, general contractors and more to engage with each other early, listen and better understand each other’s needs.
- Having a consistent regulatory framework that is not constantly being changed would assist builders in finding more efficiencies and industrializing processes.
The Whole Story:
B.C. builders and aspiring tradespeople got a glimpse into the future of construction this month as industry leaders gathered at Pitt Meadows Plumbing & Mechanical’s massive industrialized construction headquarters in Maple Ridge, B.C. for the second annual Future of Work event.
The festivities included a panel of experts sharing their thoughts on how collaboration can help accelerate innovation and improve the construction process. Attendees heard from Massive Canada CEO Gaetan Royer, Pitt Meadows Plumbing’s owner Steve Robinson, Turner senior project manager Kristine Szeto, City of Vancouver plumbing and mechanical inspections manager Phil White and ETRO Construction president Mike Maierle.
Robinson, who has led Pitt Meadows to embrace prefabrication, robotics, digital design and other technology, spoke about the role these innovations can play in the process.
“I think the big thing that the industry generally—whether it’s the mechanical industry, electrical or even the big GCs—needs to understand is that some of these next-generation technologies are allowing for a very quick, easy and fast generation of a totally collaborative model. And that’s without multiple layers of management by multiple people,” he said. “The reality is there is a huge opportunity available to totally collaborate on what the finished system looks like. This is what the reality is today, and we need to just embrace it.”
The off-site construction approach has been embraced by B.C. based prefabricated mass timber company Massive Canada. Royer explained that his goal at Massive Canada is to move as much of MEP off-site and he believes that plumbing contractors, mechanical contractors and electrical contractors should try to do the same.
“Why? Well it’s the highest cost item for a project in most multi-family buildings like a six-story, apartment building. It’s 50% of the cost and It’s mostly repeatable stuff,” explained Royer. “We need to standardize and industrialize. The only way to do that is to simplify MEP at the very base of designing the building. There should not be 20 different unit types in a 100 unit condo apartment or rental apartment. So industrialization in standardization has to be as important as aesthetics.”
White noted that municipalities are often seen as the villain in construction but stressed that Vancouver wants to support innovation and help builders build.
“In the city Vancouver is, the codes are so outdated a lot of the time, industry changes so fast and to get that into account is very, very difficult,” he said. “If you have a great product that meets or exceeds what is in today’s code, it’s very difficult to bring that into the national code, to the provincial code and then into the city of Vancouver code.”
He added that Vancouver has its own charter and own building code and is committed to making sure those innovations can be included rather than ge held back.
ETRO Construction is looking to lead the way for other general contractors by encouraging trade contractors to embrace collaboration and by developing their own standardized products.
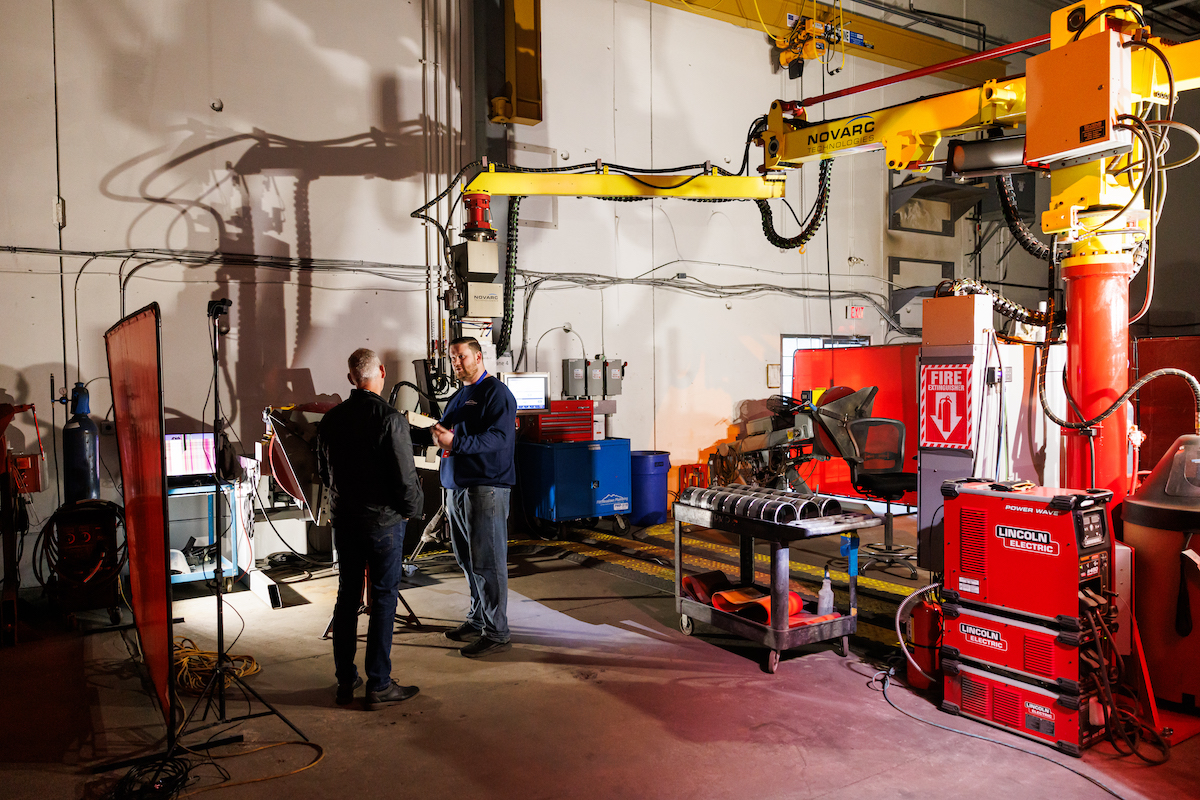
“For us, it’s a collaborative model. We don’t hard-bid any work. What we need are capable contractors of every form who can come in and collaborate on the design assist basis,” said Maierle. “If you are a mechanical contractor, it doesn’t matter. If you’re a 10-person sheet metal company or a 200-person contractor, we need you to have expertise in your office. It’s not just pricing. And second, you must have the ability to produce work off-site.”
ETRO has big plans to be a leader in collaborative, industrialized construction. Their team intends to open a collaborative trade prefabrication centre at their warehouse in Burnaby and create standardized construction products that can be used by the entire industry.
“We’re creating a space where we can bring an actual mechanical drywall steel together to build work collaboratively and so that model we think is going to help show some of these smaller medium-sized Companies how they can start to scale,” said Maierle. “If we all just continue to work the way we have from the last 100 years, we’re never going to get anywhere.”
He added that ETRO expects to have 20 to 30 products in the coming decade that other builders and contractors are going to use.
“I want to build a manufacturing machine that can not only support us, not only our local industry but a national industry that really needs progressive change,” he said.
Szeto spoke about how collaboration is becoming more and more of a requirement for big sites but can also be applied at a smaller scale.
“The projects are getting more and more complex, they’re taking up more and more physical space. There’s more systems. There’s more integration required. So collaboration is not just an advantage anymore. It’s absolutely necessary for the success of contracts,” she said. “The more and more that you do this collaboration. When you run into unforeseen problems which are bound to happen on any projects. You’re going to work through and deal with those issues far earlier than when it’s going to be too costly.”
The two-day event also sought to address construction’s workforce shortage. It included an educational showcase for students across Metro Vancouver considering a career in the trades and what the future of construction looks like.