Chandos guides fire station project across the finish line
Lloydminster’s fire station project began impacting the community long before its doors opened this year.
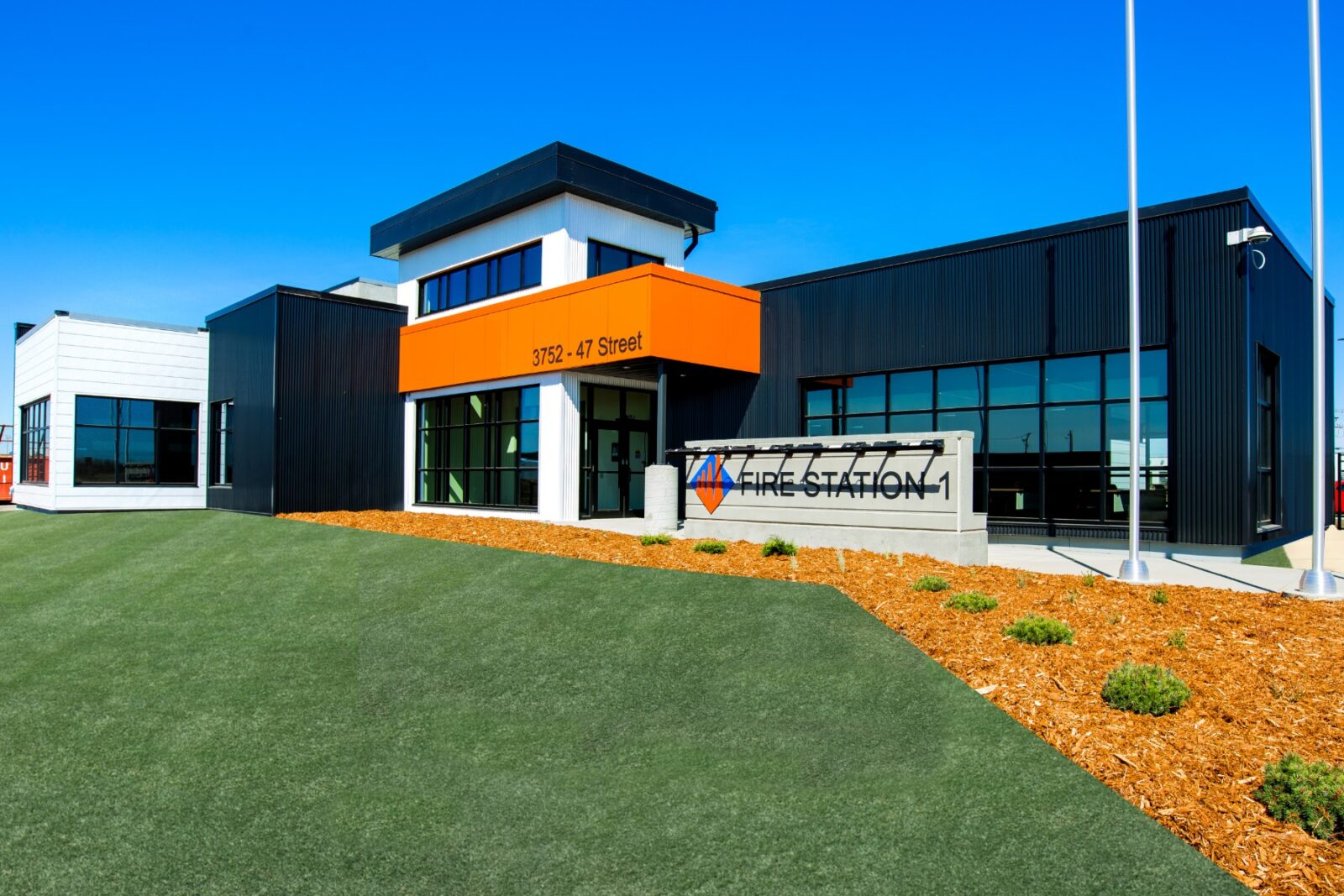
Chandos had to navigate cashflow and supply chain challenges while working on an Alberta fire hall project. – Chandos Construction
Key Takeaways:
- Social procurement and sustainable development were major parts of Chandos’ approach to a new fire hall in Lloydminster, Alta.
- The project also had to address supply chain issues and a contractor’s cash flow problems.
- Despite these challenges, the project was completed without significant delays.
The Whole Story:
Chandos, the project’s builder, explained in a web post that its team drew on social procurement and sustainable development during the build process so the community could benefit.
Roughly 90 per cent of the building’s materials were bought locally, including lumber, insulation, membrane, masonry and concrete. The team also focused on drawing from the nearby labour pool, hiring five subtrades locally.
“The team worked with various agencies to provide opportunities to at-risk individuals,” said Chandos project manager Michael Lewis. “We also collaborated with the local construction association to ensure local vendors were included as much as possible.”
The team also worked to divert nearly 65 per cent of waste from the project.
The project was not immune to supply chain issues that have been plaguing the sector. When procuring the structural steel and precast portions of the build, Chandos was informed that the roof joists that would be required had a lead time of more than 20 weeks. The wait would have delayed final turnover on the project by nine months.
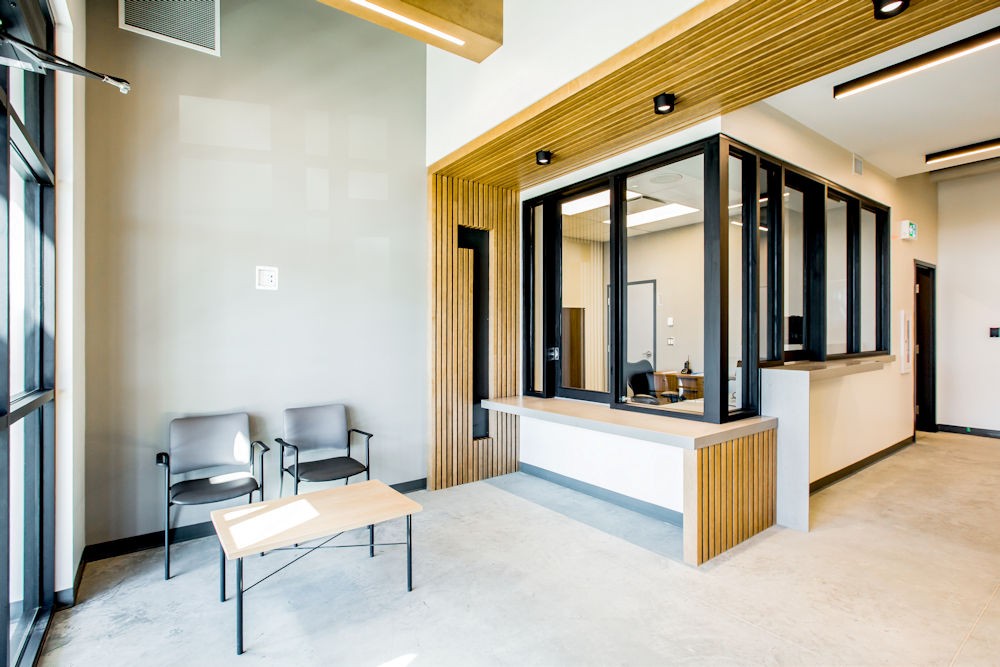
“To mitigate this issue, we went back to the bidders and had them make suggestions,” wrote the builder. “We were able to have the building redesigned structurally by our steel contractor using materials that were available, and then we were able to have the structural steel and precast contracted to be onsite by a specific date.”
While the move secured the schedule, it came at a premium of $250,000. Despite the cost, Chandos said that the reasoning behind it was thoroughly discussed and easily approved by the client.
The project also experienced delays for the main air handling unit, which the mechanical contractor said would be arriving much later than expected. Crews would need to wait to complete the structure and roofing in that section of the build.
“This would have delayed all of the work in the main mechanical area and would have created a domino effect on other contractors,” wrote Chandos.
The team worked with the mechanical contractor and the site superintendent to devise a plan. Crews left a wall section unbuilt so that the equipment could be loaded into the building after the main structure was in place. This allowed for all of the additional work to be completed in that specific area. And, when the air handling equipment arrived, it was installed and the wall sections were closed up.
The project also had to mitigate cash flow issues. The team discovered the project’s drywall contractor was having difficulties and a lien was placed on the project by a rental company due to some unpaid bills.
Chandos assisted by clearing some of the debts the contractor had. The company also had the lien cleared all while keeping the client in the loop throughout. With the issue resolved, it caused no delays.