720 builds legacy and housing with historic Maritime modular project
The six-storey Malpeque buildings are creating modular capacity on the East Coast and breaking records.
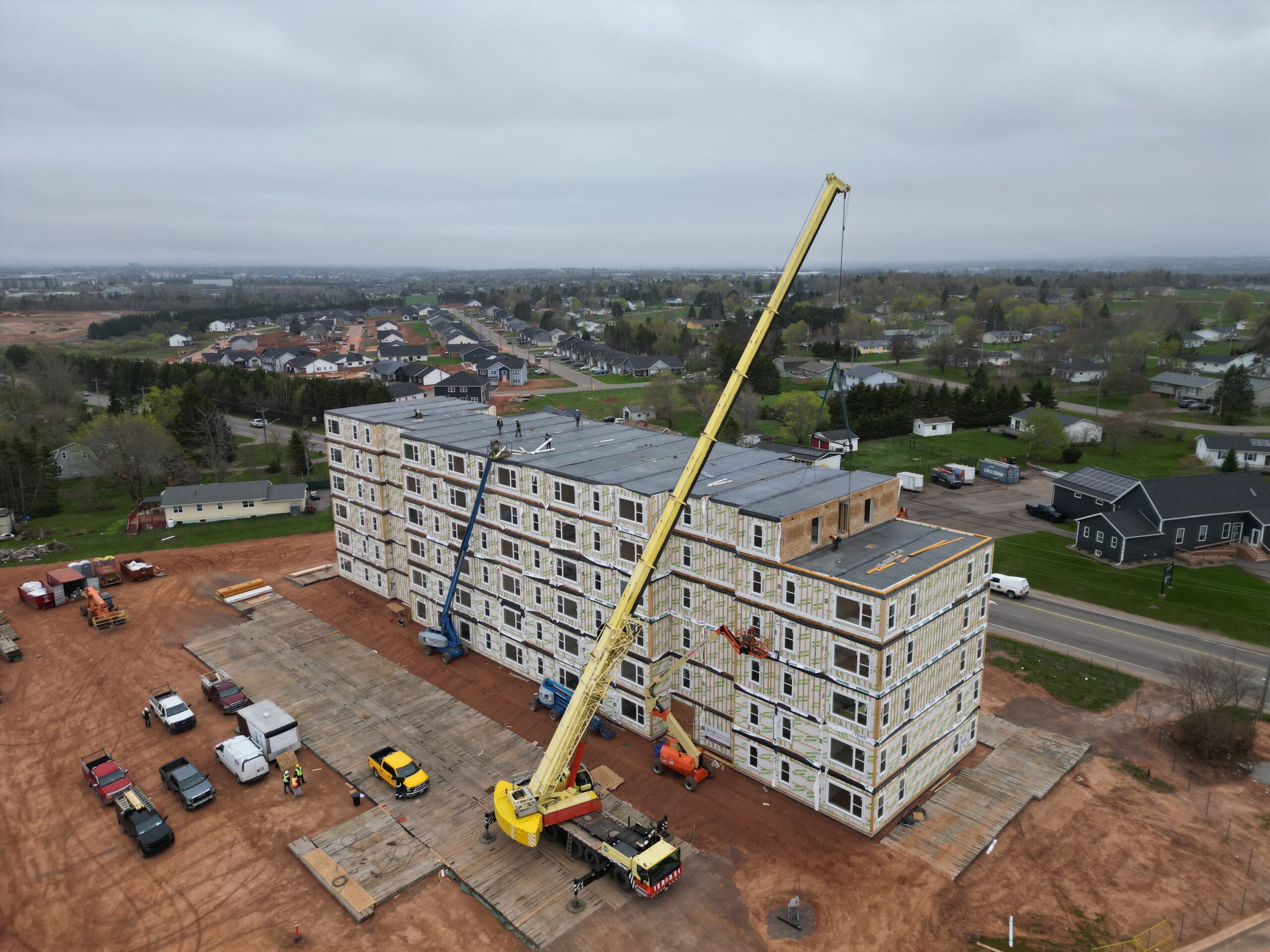
History is being built right now in Charlottetown, PEI.
Crews are assembling Canada’s largest modular apartment complex ever and experts hope it could help show the entire industry what’s possible with the right team.
The Malpeque apartment project includes two six-storey buildings: one is an 82-unit seniors’ apartment, and the other is a 63-unit family-oriented building. Both are being built for the Province of Prince Edward Island and the seniors’ building is the first one under construction.
Leading the effort is 720 Modular. Their approach was to gradually build modular capacity in the region by working with local builders. It’s their sixth project in PEI and it’s given contractors a chance to learn the ropes from industry veterans, 720 Founder and CEO Troy Ferguson and his business partner, Craig Mitchell, the company’s Project Development Lead. As the pair enters the latter half of their careers, they hope these seeds can create a legacy for years to come.
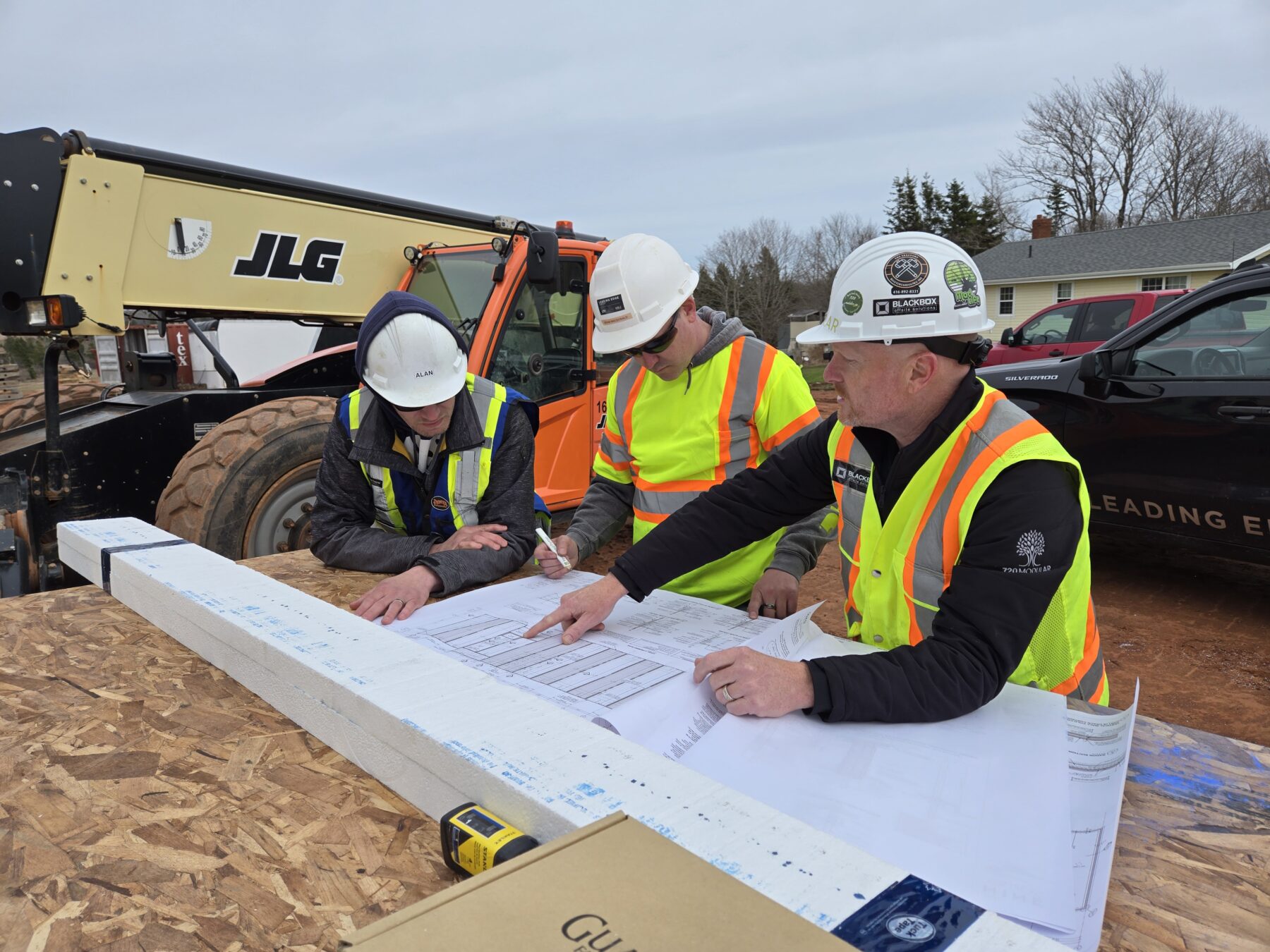
“What you’re seeing now is a strong team in PEI that’s been able to deliver multiple modular projects,” said Craig Mitchell, Project Development Lead at 720. “We’ve got the same design team from the beginning, and the expertise they’ve built allows the design process to move faster. There’s a real spirit of collaboration and culture now. Everyone knows each other—it’s more like working with friends.
Ferguson explained that the Province first partnered with them on Fitzroy, a multi-storey housing project, and the relationships have grown from there.
“They were at the table during pre-construction, seeing how modular works and watching their local businesses do the work with us guiding the process,” he said. “That early involvement facilitated future projects, including homeless shelters with repurposed assets from Western Canada. That relationship eventually led to this—the largest modular housing project in the country. The government had been keen to learn along with everyone else.”
The site sits on the outskirts of Charlottetown, allowing the team to plan for cranes, laydowns and access. But the true challenge is manufacturing. Malpeque is using substantial annual capacity of the region’s largest modular factory, something that few factories are willing to commit to a single client. To deal with this, work on the buildings has been broken into phases.
Another major challenge of the project is pushing the limits of what’s allowed—six storeys is the maximum for light wood-frame construction under the code and most modular projects in Canada are four storeys or under.
“You really have to reinforce the first and second storeys to support everything above. It’s not just a challenge—it’s a discovery process,” said Ferguson. “Now that we’ve done it, we can share that knowledge. Hopefully it kickstarts more mid-rise projects using conventional factory-ready materials.”
Despite this, one of the key advantages of modular construction is the ability to conduct certain offsite activities in parallel with site preparations. In this case, factory processes commenced while the project team continued working through final permit approvals. Foundations were completed just before Christmas, ensuring the site was ready for module delivery by early spring.
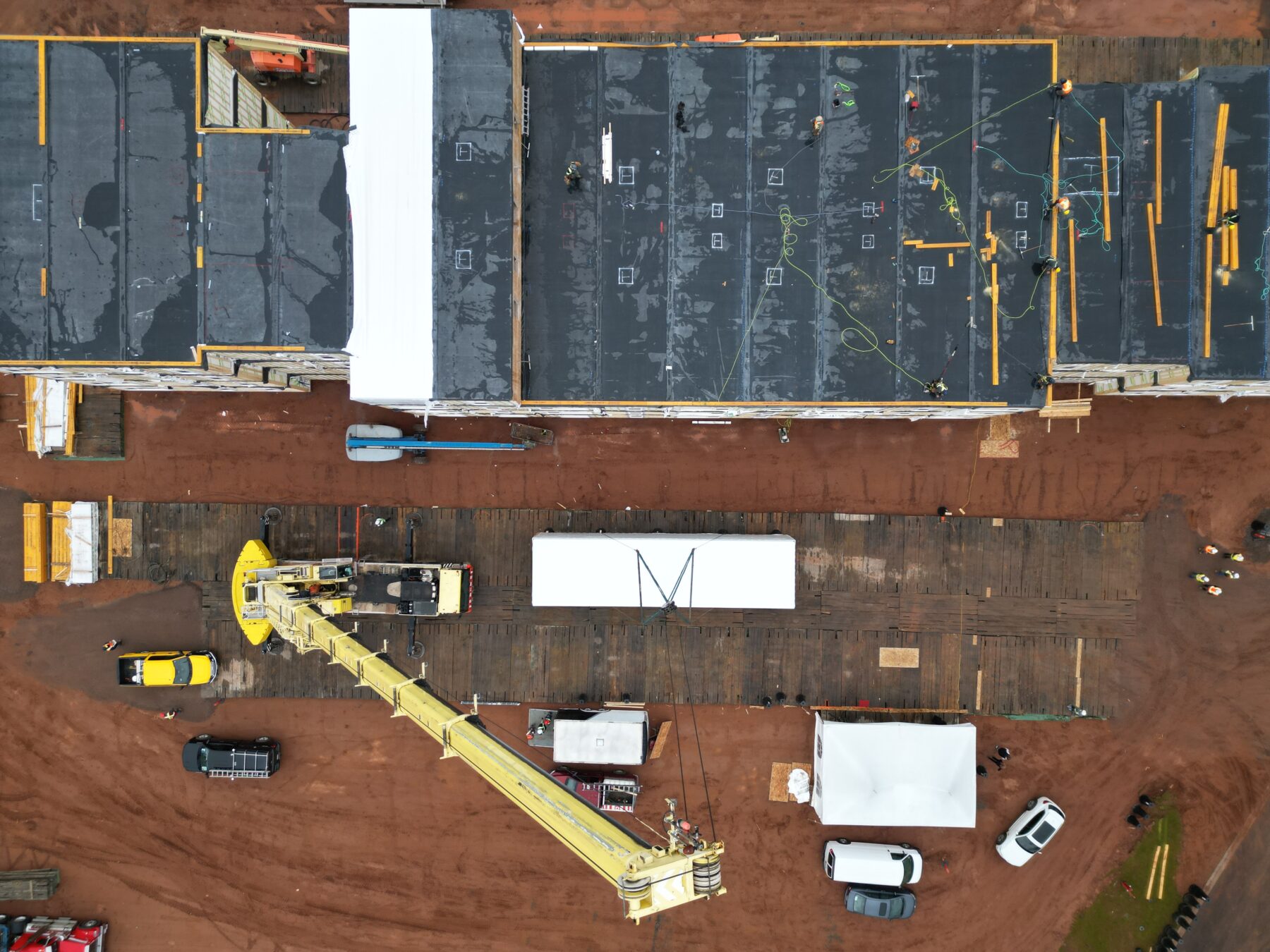
“In the field, we’re only going to be on-site for six months. From permit to building turnover—roughly five to six months. Compare that to a conventional timeline of 14 to 15 months,” said Mitchell.
There’s also schedule and cost certainty. Every design decision is made upfront—right down to coat hooks. By the time production starts in a controlled factory environment, the budget is essentially baked in.
“The only change during our design phase was a $6,000 addition for additional shower heads in accessible bathrooms. That’s it,” said Ferguson. “And because of that certainty, we locked in our craning date eight months ahead of time. That level of precision is possible in this emerging industry while using the same traditional construction professionals and materials.”
For industry veterans like Ferguson and Mitchell, Malpeque is more than a project. It’s an opportunity to pass down their modular construction knowledge when the country needs it the most.
“We’re creating a playbook as we go—lessons learned, the architecture of a business model that uses existing resources in a new way,” said Ferguson. “We hope it’ll guide others—contractors, developers, factories, and owners.”
Mitchell noted that 720 is already working on replicating their model in Ontario.
“We’re trying to give the industry a case study it can adopt and scale,” he said. “We think we’ve found a model to scale housing in Canada—and we want to share it.”